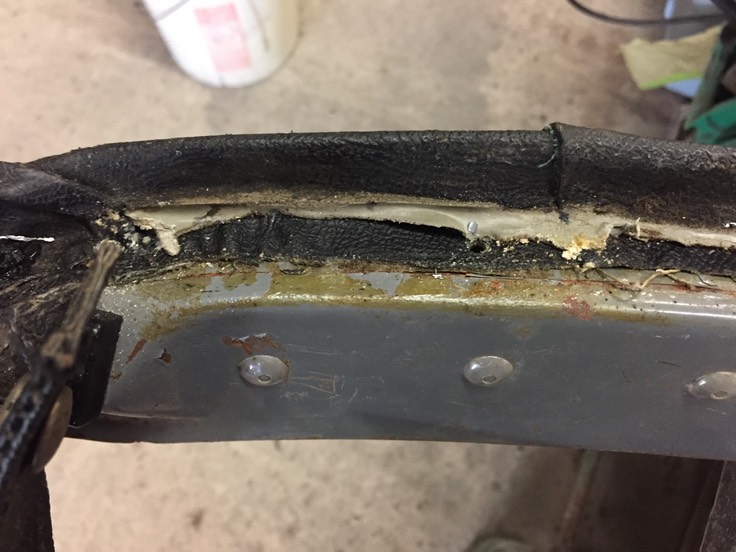
Drilling out the pop rivets exposed how the factory finished the corners: Quickly! The hood material was allowed to bunch up and they just smashed it down with the aluminum strip. They also added a bead of bedding compound to stop water from working its way between the aluminum and the hood material. This is the same goop that the factory sealed the joints at the corners of the windscreen . Even after 40 years, the stuff is still flexible. I generally omit this step, but there is no reason you could not use the same 3M Bedding Compound that we use on windscreens. However, if the hood is fitted well and the seal is fitting correctly on the upper ledge of the windscreen frame, they don’t really leak.
This is also a nice view of the plastic plugs that fill the three threaded holes not used for Stow Away hood bows. I believe they are called blind expanding-shank rivets, where you bonk in the little plastic center to spread the feet that hold them in place.